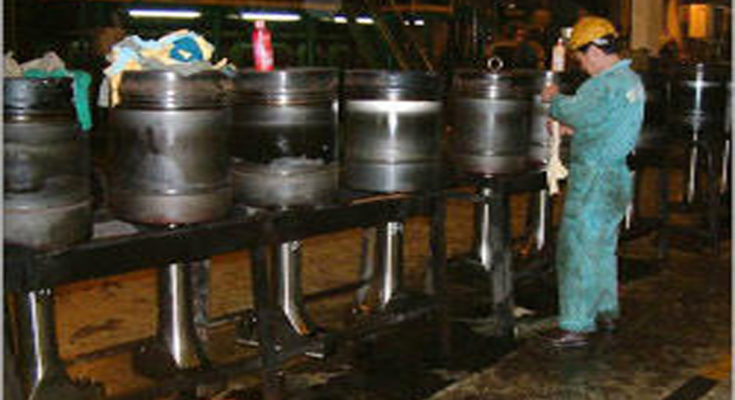
Rudolf Diesel
The diesel engine (also recognized as a compression-ignition or CI engine) is an internal combustion engine in which ignition of the fuel that has been injected into the combustion chamber is caused by the high temperature which a gas achieves (i.e. the air) when greatly compressed ( adiabatic compression ). Diesel engines operate by compressing only the air. Then in that case the initial stress ought to be sixty-four atmospheres, or for 800° centigrade the pressure ought to be ninety atmospheres, and so on. Into the air thus compressed is then progressively introduced from the exterior finely divided fuel, which ignites on introduction, since the air is at a temperature far above the igniting-point of the fuel.
Having said that the original cycle proposed by Rudolf Diesel in 1892 was a continual temperature cycle (a cycle based on the Carnot theory) which would demand much greater compression than what is …
Rudolf Diesel Read More