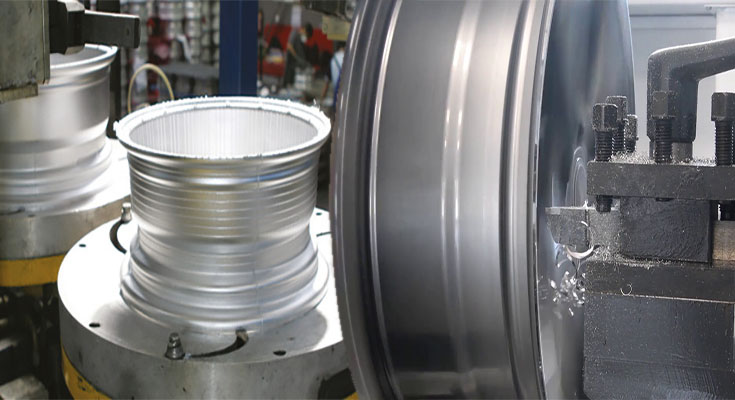
The Manufacturing Process of Alloy Wheels
Among the many aspects that make up the manufacturing process of alloy wheels are the cost and rigidity of wheels. The manufacturing process also includes die- casting technology. Finally, alloy wheels undergo a heat treatment process to make them durable and resistant to corrosion. To learn more, read on. This article will discuss some of the main factors that affect the cost and rigidity of alloy wheels. The manufacturing process also includes the costs of alloy wheels, the rigidity and cost of die-casting technology, and the Heat treatment procedure.
Cost of alloy wheels
Alloy wheels are more expensive to manufacture than standard steel wheels, so they are often marketed as optional extras or part of a higher-priced trim package. Increasingly popular in recent years, alloy wheels are not factory options on all cars. Until 2000, they were usually reserved for expensive luxury and sports cars, but are now becoming more …
The Manufacturing Process of Alloy Wheels Read More